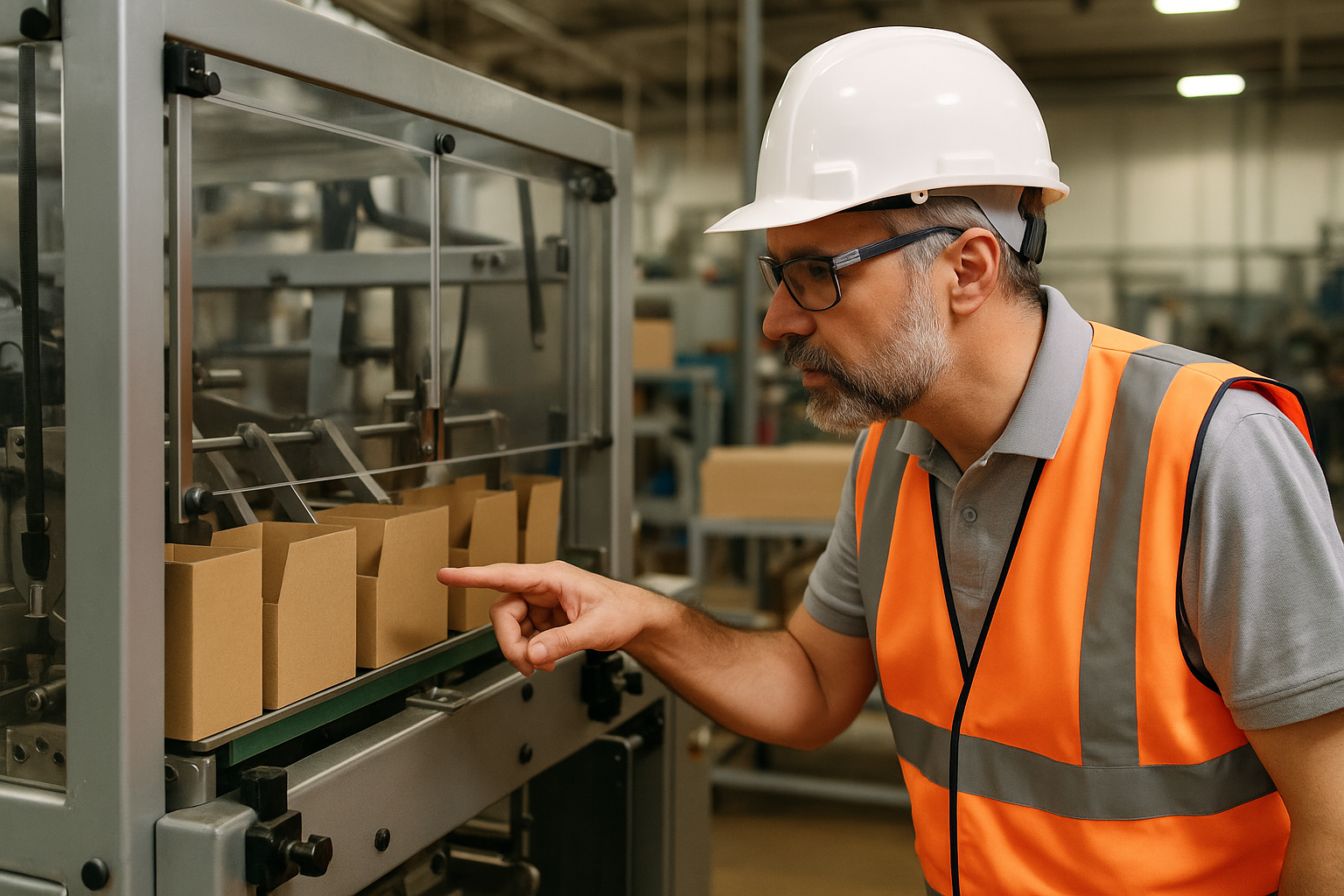
Uptime Improved Carton Machine
Efficiency of carton machines increased
Lean Six Sigma might sound complex if you’re unfamiliar with it, but when applied correctly, it can transform how a business operates, leading to substantial financial benefits. In this article, we explore a practical example of how Lean Six Sigma was used to boost machine uptime at a packaging facility, offering insights into the challenges faced, the solutions implemented, and the impressive results achieved.
The Challenge at Hand
This project was centered around improving the uptime of carton machines at a packaging facility. For those unfamiliar, a carton machine is a specialized piece of equipment used in the packaging industry to assemble and fill cartons with products, which are then sealed and prepared for distribution. These machines are vital in high-volume production environments, where any downtime can lead to significant disruptions and increased costs.
At the facility in question, downtime on the carton machines was causing a reduction in overall production output, leading to higher labor costs and missed opportunities for revenue. The project aimed to address three key issues: major sources of downtime, minor sources of downtime, and overall machine utilization.
By tackling these areas, the goal was to improve production efficiency, standardize machine operations, and ultimately increase profitability. The baseline data for this project was collected from the facility’s internal systems, focusing on the period from January to February 2024.
Building the Right Team
A critical factor in the success of any Lean Six Sigma project is assembling a capable and motivated team. The project leader carefully selected a team of experts from various departments, including Inventory, Quality, and Planning.
Each member brought valuable expertise to the table, which was essential for addressing the project’s complex challenges.
One of the early decisions was to broaden the project’s scope to include all carton machines at the facility, rather than focusing on just one production line.
This approach allowed the team to apply process improvements across the entire operation, maximizing the impact and ensuring more consistent results.
Applying Lean Six Sigma Tools
The project followed the DMAIC (Define, Measure, Analyze, Improve, Control) methodology, which is a core project management structure within Lean Six Sigma. Among the various tools used, the Pareto Diagram proved to be particularly effective. This diagram helped the team identify the primary causes of downtime, enabling them to focus on the most significant issues first.
During the implementation phase, the project leader developed an Excel-based tool for tracking downtime, which was used to monitor progress and keep the team informed. This visual tool was instrumental in maintaining alignment and ensuring that everyone was aware of the project’s status and successes.
Overcoming Obstacles
No project is without its challenges, and this one was no different. One of the major hurdles was changing the habits of the machine operators, who were accustomed to certain routines. Initially, there was resistance to adopting new procedures, but this was addressed through ongoing coaching and reinforcement. The project leader and supervisors were present at the start of shifts to ensure that the new processes were being followed correctly.
Another challenge involved the time required for coaching and education, which took longer than anticipated. To address this, the team implemented a “kaizen blitz,” a rapid and focused improvement effort aimed at accelerating machine operation education and preventive maintenance.
Achieving Sustainable Results
The results of the project were outstanding. Over the six-month period, the efficiency of the carton machines increased from 99% to 110%, while downtime was reduced from 12% to just 4.5%. These improvements translated into significant financial savings, with the facility saving over $33,000 per month.
To ensure these gains were maintained, the team conducted daily reviews of downtime metrics and made immediate adjustments when necessary. This proactive approach was key to sustaining the improvements over time.
Key Takeaways
This project provided several valuable lessons for those new to Lean Six Sigma.
First, consistent monitoring is crucial for identifying and addressing issues as they arise. Second, effective coaching, training, and communication are essential for getting team members on board with new processes. Lastly, tools like the Pareto Diagram are invaluable for pinpointing and addressing the most significant opportunities for improvement.
For anyone considering a Lean Six Sigma project, this case study illustrates the practical application of these methods in a real-world setting. It highlights the importance of thorough preparation, having the right team, and being ready to adapt to challenges as they come. With these elements in place, Lean Six Sigma can drive significant improvements in efficiency and profitability, even in complex operations like those found in the Consumer Goods industry.
Conclusion
The “Increased Carton Machine Uptime” project is a textbook example of how Lean Six Sigma can be applied to achieve meaningful business outcomes. By reducing downtime and increasing machine efficiency, the project not only met its goals but also delivered substantial financial benefits. For those new to Lean Six Sigma, this project offers a clear, detailed guide to what’s involved and the kind of success that’s possible with the right approach and commitment.
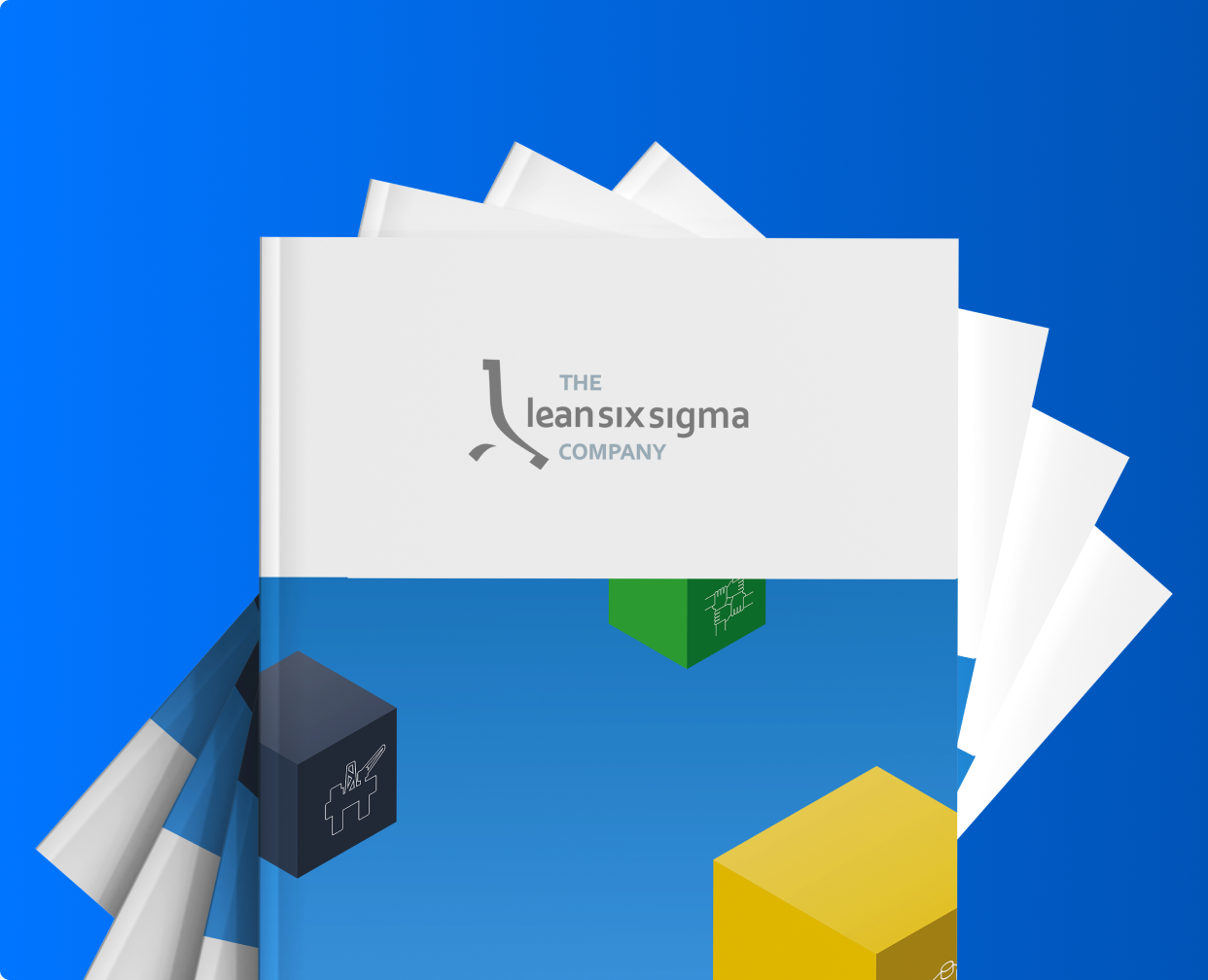