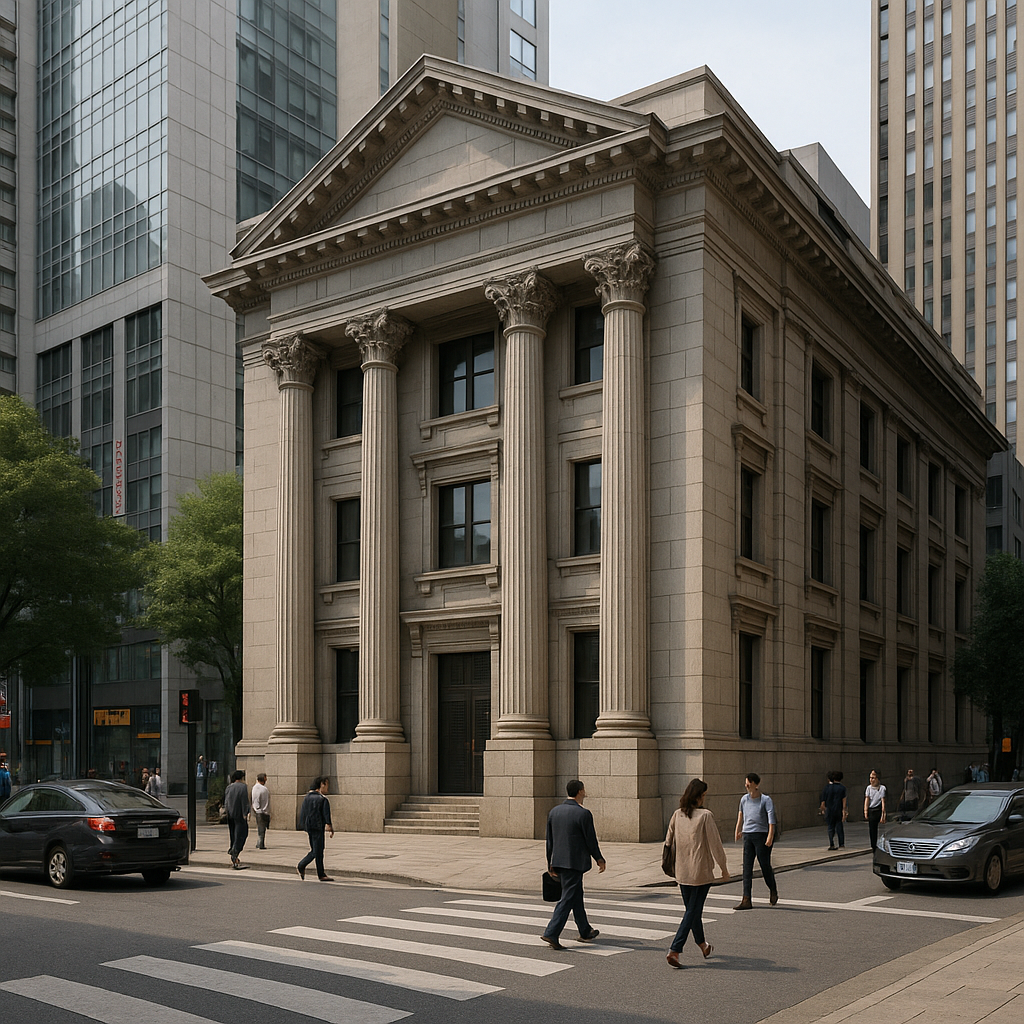
Improving Covenant Monitoring in a Bank: A Practical Lean Six Sigma Journey
In today’s competitive financial sector, efficiency is key. Banks often handle complex processes such as covenant monitoring, which involves ensuring borrowers comply with the terms of their loans. At one financial institution, the delays in this process were starting to affect service delivery. Enter Lean Six Sigma, a proven methodology designed to streamline workflows and eliminate waste. This article details how a Lean Six Sigma Black Belt project addressed the delays and inaccuracies in the bank’s covenant monitoring response process, and the lessons learned along the way.
Identifying the Problem
The central issue was significant delays in responding to covenant monitoring requests made by regional managers (RMs) and credit officers. At the project’s outset, the average response time was 9.78 days—far too long in a fast-paced industry. Additionally, errors in the responses—critical in covenant monitoring—were causing further complications. These delays and errors impacted the bank’s ability to stay compliant and serve its clients efficiently.
The project team, led by a Black Belt, focused on reducing the response time to under 7 days while also minimizing inaccuracies. The business goal was clear: to streamline the process, meet deadlines, and improve accuracy. The project sponsor, the Deputy Manager of the Covenant Monitoring Unit, was fully supportive of the initiative, providing essential guidance and resources throughout the project.
Assembling the Team
Selecting the right team members is critical to the success of any Lean Six Sigma project. In this case, the team was composed of subject matter experts from the covenant monitoring unit, including one staff member skilled in Excel automation and another who had undergone Yellow Belt training. This diverse skill set proved invaluable as the team needed to analyze data, map processes, and implement solutions effectively.
The willingness of the team members to work collaboratively was another key factor. The process owner was highly motivated to resolve the issues, and the hands-on involvement of the unit’s staff meant that real-world challenges were easily identified and addressed. Having a motivated team allowed for quicker problem-solving and more innovative solutions.
The Lean Six Sigma Approach
The project followed the DMAIC methodology—Define, Measure, Analyze, Improve, and Control.
This structured approach ensured that every aspect of the process was examined in detail, and solutions were implemented in a systematic way.
Define Phase
The project team used tools like SIPOC (Suppliers, Inputs, Process, Outputs, Customers) and Value Stream Mapping (VSM) to map the covenant monitoring process and understand the delays. These tools helped the team visualize the entire process, from when the covenant monitoring request was generated to when the response was delivered.
The main problems identified were bottlenecks in the feedback process, inefficient communication between departments, and errors in the monitoring responses. By defining these issues early, the team could focus its efforts on resolving the most critical pain points.
Measure Phase
During this phase, the team collected historical data to assess the average response times and the frequency of errors. Sigma levels—a metric used in Lean Six Sigma to measure the quality of processes—were calculated. Initially, the process was performing at a Sigma level of 3.88, indicating room for improvement.
To measure progress, the team set a clear goal: reduce the response time from 9.78 days to under 7 days and improve the Sigma level to 4.0 or higher. Data collection was automated wherever possible, reducing the risk of human error.
Analyze Phase
Using tools like Fishbone Diagrams and Pareto Charts, the team identified the root causes of the delays. They found that communication breakdowns between regional managers and the covenant monitoring unit were a major issue. Moreover, the workflow itself was overly complex, leading to errors in the responses.
Statistical analysis also revealed that 60% of the issues were caused by just a few factors, aligning with the Pareto Principle (the 80/20 rule). This analysis allowed the team to prioritize the most critical problems.
Improve Phase
The team implemented several changes to streamline the process. Workflow automation was introduced to minimize manual steps and reduce errors. The Excel automation expert on the team developed tools to standardize responses and reduce response times.
Additionally, the team established clearer communication channels between departments. Regular update meetings with regional managers ensured that everyone was on the same page, reducing delays caused by miscommunication.
The project’s results were impressive: response times dropped from 9.78 days to 4.21 days, and the Sigma level improved from 3.88 to 4.02. This improvement not only met the project’s goals but exceeded expectations.
Control Phase
The final phase of DMAIC involved ensuring that these improvements would be sustained over time.
A control plan was implemented to monitor the process and ensure that the improvements were maintained. This included assigning a dedicated resource to oversee the covenant monitoring process and regular audits to ensure that response times and accuracy remained at acceptable levels.
To further solidify the changes, Standard Operating Procedures (SOPs) were updated, and training was provided to all relevant staff. By institutionalizing these changes, the bank ensured that the improvements would be long-lasting.
Overcoming Challenges
No Lean Six Sigma project is without its challenges. In this case, one of the initial obstacles was resistance from a Deputy Manager in the covenant monitoring unit. Convincing him to fully support the project took time and careful communication. By outlining the project’s benefits and showing early wins during the pilot phase, the team was able to bring him on board.
Another challenge was accessing the necessary data for analysis. The human resources department was reluctant to provide historical data for analysis due to confidentiality concerns. However, after explaining the purpose of the data and the measures that would be taken to ensure privacy, the team was able to secure the necessary information.
Lessons Learned
Several valuable lessons emerged from this project. First, constant follow-up and communication with team members are crucial. Keeping the team focused on the project goals helped to maintain momentum and ensured that deadlines were met. Second, having the full support of top management from the beginning of the project is essential for success. Regular updates to the project sponsor and other stakeholders kept everyone aligned and prevented misunderstandings.
Finally, it became clear that involving the process owner and end-users from the very start is key.
Their input ensured that the solutions implemented were practical and that the changes made would stick.
Conclusion
This Lean Six Sigma project demonstrates the power of structured problem-solving in streamlining complex processes. By reducing response times and minimizing errors, the bank not only improved its operational efficiency but also set the stage for long-term success. The financial benefits, estimated at over $40 million, highlight the tangible value of Lean Six Sigma in the financial industry.
For those unfamiliar with Lean Six Sigma, this project shows how practical tools and methods can be applied to solve real-world problems and drive significant improvements.

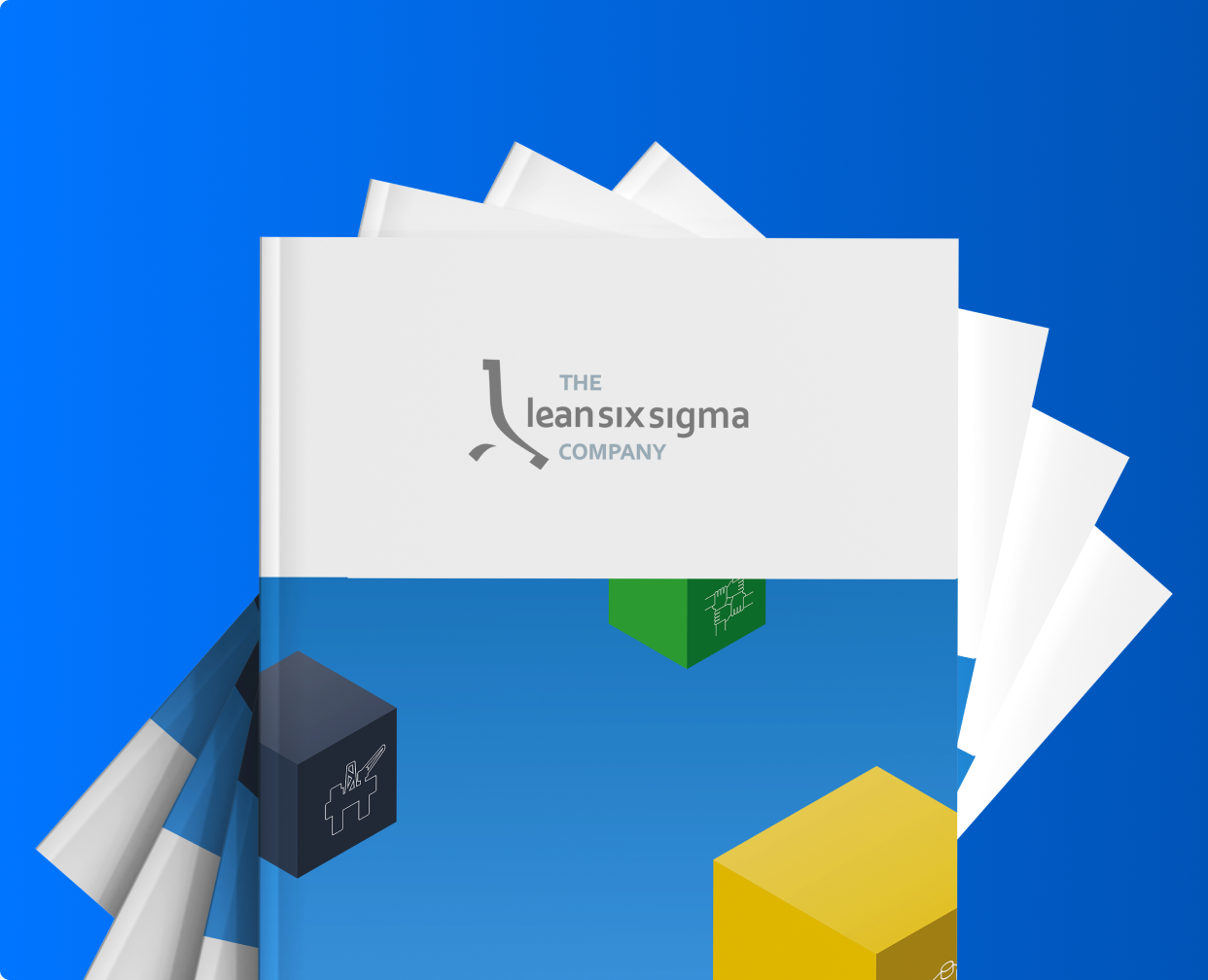